Hanover Housing Association
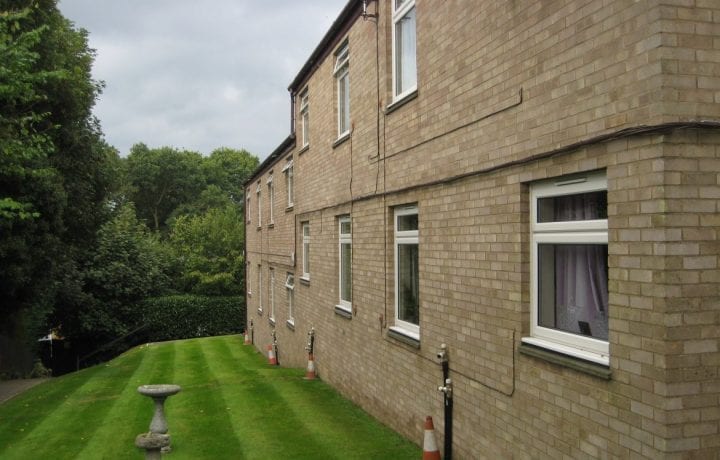
Ground Source Review: Hanover, Ashfield Court.
Two-storey flats in hard-to-reach cul-de-sac combat fuel poverty and high carbon emissions with Kensa shared ground loop array ground source heat network.
In just ten weeks, twelve communal boreholes totalling 1700 metres deep were drilled, 92 night storage heaters and 22 vented hot water cylinders were removed, and twenty-three ground source heat pump systems complete with unvented hot water cylinders were installed along with 115 new radiators.
Ground Source Review: Hanover, Ashfield Court
Ashfield Court is a block of 22 flats with one site office. The 2-storey block was built in 1977 and is of traditional brick construction. In recent years, Hanover Housing Association has installed loft insulation, cavity wall insulation and double glazing to improve the thermal performance of the buildings. There was little more that they could do to make the fabric more energy efficient.
However, all the properties still had the original electric night storage heaters which were nearing 40 years old and were well past the end of their useful life, and so needed replacing. Consequently, despite the energy efficiency improvements made by Hanover, tenants were suffering from high fuel bills.
Additionally, the poor environmental performance of the heating system was dragging down the Environmental Impact rating of these flats. Hanover were keen to reduce their carbon emissions while at the same time addressing fuel poverty.
Hanover had this site earmarked for “fuel switching”, meaning that they were intending to install a new mains gas supply to the site with individual boilers in each dwelling. However, the near-by gas main did not have sufficient capacity to allow the flats to be added to it. Consequently, this meant bringing in a new gas main from over 500 metres away. Additionally, due to the design of the flats it was not easy to find suitable locations for the flues. This ruled out gas as a cost-effective solution.
Hanover decided to look at other options for heating the flats and it became clear that the micro-district ground source heat pump solution proposed by Kensa was the best solution. Hanover’s technical team had been aware of this solution since attending a conference in summer 2015 that documented the successful installation of nearly 200 heat pumps into properties owned by Trent & Dove Housing Association. Hanover were keen to adopt this technology into their own housing stock.
Although the up-front capital cost was more, the potential to receive upfront ECO funding provided by Kensa’s unique partnership with EDF Energy, along with twenty years of Non Domestic RHI (this scheme has closed) income, plus significantly lower maintenance costs, meant that this system would more than pay for itself in the long-run. It was the cheapest long-term solution.
In addition, the running costs for the residents would be the lowest possible helping to address fuel poverty. All of this was enough to convince the Hanover board to opt for Kensa micro-district ground source heating.
The main aims of the project were to:
- reduce energy bills and so tackle fuel poverty;
- improve thermal comfort and so increase tenant health and well-being;
- make the properties more lettable thus reducing void periods and increasing rental income;
- reduce carbon emissions and so improve the Environmental Impact rating of Hanover’s housing stock;
- generate an ongoing income stream for Hanover HA allowing them to further invest in energy efficiency measures across their housing stock.
Winston Williams, Property Director at Hanover Housing Association said:
Hanover were keen to adopt micro-district ground source heat pump technology into our housing stock as we felt it provided a cost effective and long-term solution, and means residents will save money on their heating bills as a result. As well as being able to monitor running costs and ensure the systems are performing efficiently, the new scheme will save nearly 1,900 tonnes of carbon emissions during its lifetime, so it really is a win, win for everyone.
The process
Kensa Contracting Ltd were appointed by Hanover as the principal contractor for this project. Kensa has achieved safe contractor accreditation which gave Hanover confidence that the project would be delivered on time and on budget. Additionally, Hanover were impressed with Kensa’s track record of completed projects.
Kensa designed the whole project and were responsible for the complete installation, commissioning and MCS accreditation. Kensa appointed experienced sub-contractors to carry out the ground works who have worked in partnership with Kensa for a number of years on other social housing projects. For the internal works, Kensa sub-contracted one of Hanover’s approved M&E framework contractors, SSE Contracting. This has the advantage of working with a contractor familiar to Hanover and its tenants; they can also take over the long-term maintenance of the system once Kensa’s two-year warranty period has passed.
Tenants remained resident in their homes throughout the whole project. A comprehensive tenant liaison programme was delivered to ensure tenants were well-informed in advance of the project and afterwards, and educated on how to use their new simple-to-control heating system.
During the removal of the old night storage heaters, even though the project took place during some of the hottest weather of the year, electric room heaters were left with the residents just in case they required some temporary heating until the heat pumps were up and running, which typically took 2-3 days. Residents were never without domestic hot water overnight.
Kensa’s holistic approach also encompassed securing funding for the scheme, working with Hanover to secure the ECO funding and the RHI (this scheme has closed) income, with continued support as required for ongoing RHI (this scheme has closed) obligations.
The system design
In total, 11 networks were installed for the 22 flats with a separate system for the office.
Each micro-district heat network consists of two flats sharing one borehole. One flat is on the ground floor and the other is directly above it on the first floor.
The borehole depths were designed for each network based on the peak heat losses and space heating and domestic hot water energy requirements of each flat. Twelve boreholes were drilled in total, with depths of up to 154 metres. Trenches were dug from each borehole back to the boundary of the flats to install the headering pipework and the manifolds.
The plumbing team then took over and installed pipework from the manifold at the boundary of the flats to each heat pump location. For most pairs of flats, this ground side pipework runs up the rear of the building into the loft. This pipework is covered with white UPVC trunking to blend in with the windows. Once in the loft, the ground side pipework runs down to the first floor flat and then continues down to the ground floor flat.
Within each flat, a Kensa 6kW Shoebox Twin heat pump and new 150 litre unvented hot water cylinder were fitted in the airing cupboard. This provides each tenant with individual control and, importantly, individual billing. The circulating pumps to the boreholes are individual to each unit, so there are no centralised running costs for Hanover to manage and bill.
With no need for a plant room, Kensa’s solution overcomes the drawbacks of traditional “central plant” district heating systems. Efficiency is not compromised by heat loss in the distribution pipework and there is no need to meter and apportion energy bills between dwellings, thus avoiding the need to comply with Heat Network (Metering & Billing) Regulations 2014.
Within each flat, new radiators were installed in the space vacated by the previous night storage heaters, so tenants do not need to adjust the layout of furniture in their room and re-decoration is not required. The radiators have been designed to operate at a maximum flow temperature of 50°C to ensure the heat pumps will operate at a high seasonal efficiency. All radiators are of the double panel, double convector type. Control of the system is carried out simply using a twin channel programmer and a dial thermostat. This is important as all the tenants are over 60 years old and required an efficient yet simple to use system.
The benefits
It is expected that, on average, each tenant will save £352 per year on their fuel bills.
Additionally, the new system is simple to control and allows residents to switch the heating on when they require it. This is a significant improvement over the old storage heaters which stopped emitting heat by mid-afternoon, forcing residents to use stand-alone electric room heaters to stay warm. As well as improving the comfort of all residents, it is expected that the new heating system will improve their health and well-being as well.
Furthermore, housing associations like Hanover are recognising that energy efficiency measures help to reduce rent arrears and void periods, as tenants naturally are happier, and healthier in warmer, affordable to heat homes.
We went on holiday while the whole installation was going on – we came home after 1 month and everything was perfect.
Great heating! Instant heat what more could you ask for.
Contractors made the whole process as painless as possible. Well done Hanover for looking at something new, ground source heating.
Good, controllable, instant heating, and hopefully cheaper.
Very interesting seeing the drilling. Contractors great, always had time to explain what was happening.
The borehole drillers are the most professional contractors we’ve ever had on site. They work hard all day and are doing a great job!
Key achievements
Some of the notable achievements of the project:
- All works carried out while the elderly tenants remained in their homes within 10 weeks;
- Average annual energy bill savings of approximately £350 per household (or over £50,000 across all projects) – typically up to 50% savings;
- Over the 40 year lifecycle of the GSHP systems (as defined by ECO), Hanover estimate to save approximately £1.5m compared to the gas alternative.
- Lifetime carbon savings of approximately 1,909 tonnes across the sites (or about 80 tonnes per property);
- Estimated RHI (this scheme has closed) income of over £2 million over the next 20 years from these 6 sites alone which Hanover is planning to use to invest in more ground source heat pump installations;
- Estimated ECO income of over £200,000 which will all be received within 4 months of the projects being commissioned which Hanover is able to immediately reinvest into more installations;
- Over 12,000 metres of pipework has been installed in boreholes in the ground which will now provide heating for at least the next 100 years – a fantastic infrastructure resource.
Evidence
Each system has a heat meter measuring heat produced by the heat pump and an electric meter measuring electricity consumed by the heat pump. The former allows Hanover to receive income from the RHI (this scheme has closed) for the next 20 years. The latter allows Hanover to monitor running costs and ensure the systems are performing efficiently. Meter readings from these meters are automatically e-mailed to both Hanover and Kensa on a daily basis. There is no requirement to visit site to read the meters.
Hanover has its own specialist in-house team of energy advisors. This team has already provided help and advice to the tenants at Ashfield Court to help them switch from an Economy 7 tariff (used for electric night storage heaters) to the cheapest standard electricity tariff. This team will continue to monitor the performance of the heat pumps over the coming years to measure the effectiveness of this technology at reducing tenant fuel bills.
The installation of micro-district ground source heat pump systems at Ashfield Court received ECO (Energy Companies Obligation) funding through the CERO (Carbon Emissions Reduction Obligation) stream. This funding stream has an approved OFGEM methodology for calculating the lifetime carbon savings. Using this methodology, the scheme will save 1,909 tonnes of carbon emissions during its lifetime.
Beverly Head, Hanover’s estate manager at Ashfield Court said:
Residents were apprehensive about the amount of disruption that was required on the estate to get the new heating installed; they were amazed at the drilling and just how much pipework was needed to get the heating into their flats. Contractors were sympathetic to the amount of disruption that was required and worked with the residents to ensure that they were well informed about the project at all times. Residents are now thrilled to bits with the instant heat and at a reduced price!!!
The final word goes to Peter Phillips, one of Hanover’s technical managers who is responsible for Ashfield Court:
The residents now have an affordable heating system which is expected to make a 30 per cent saving on all of their future heating and water bills plus low maintenance costs for a least 20 years.
Along with that, over the lifecycle of the systems’ installation, there will be an income benefit to Hanover thanks to the Governments’ RHI (this scheme has closed) grant, this means a win – win situation for all.
The controls are accessible and really easy to use. For Hanover, being an organisation that specialises in housing for older people, the low surface temperate of the radiators is a real positive. The installation took approximately 10 weeks, the drilling was the more intrusive and disruptive, but four weeks after completion the grass and landscaping has recovered and there is barely any visible sign of any previous groundwork.
- Winner: Retrofit Project of the Year (H&V News Awards 2017)
- Winner: Most Innovative Retrofit Scheme (Housing Innovation Awards 2017)
- Shortlisted: Best Partnering Scheme (Housing Excellence Awards 2017)
Hear what the judges at the Housing Innovation Awards 2017 had to say about this award winning project:
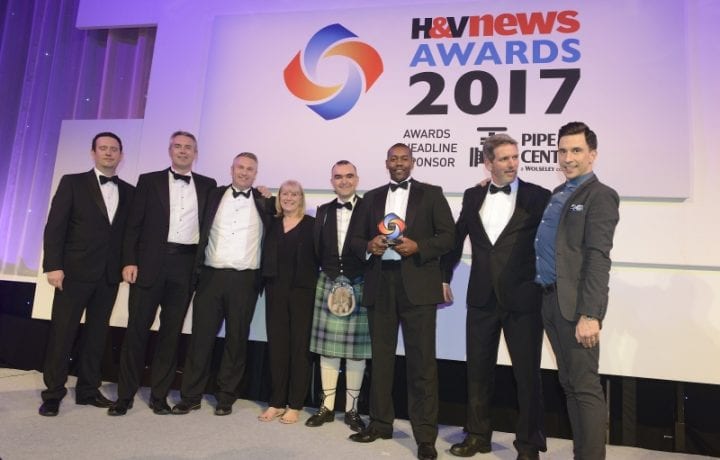
Kensa Heat Pumps and Hanover win Retrofit Project of the Year at the H&V News Awards 2017
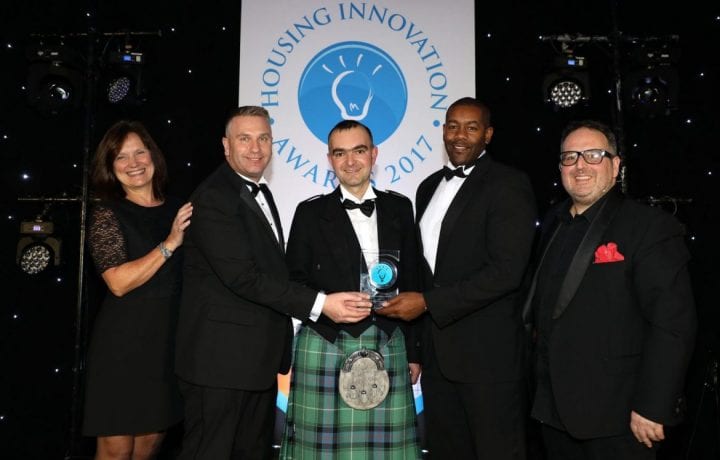
Margaret Allen (Judge), Peter Philips (Hanover), Stuart Gadsden (Kensa), Winston Williams (Hanover), Justin Moorhouse (Host)
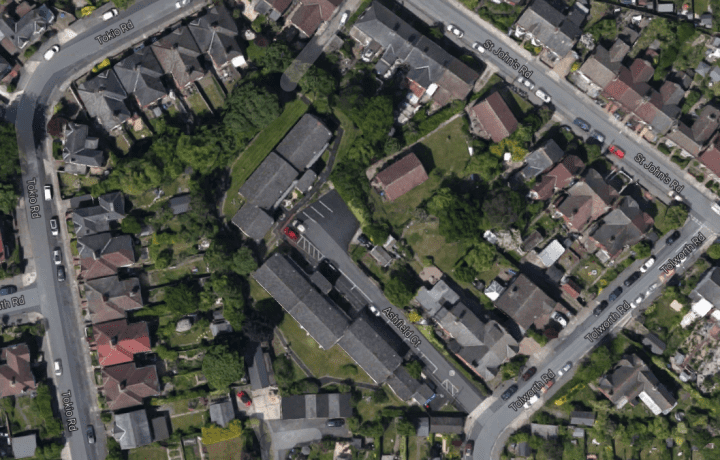
Ground Source Review: Hanover, Ashfield Court - Aerial View
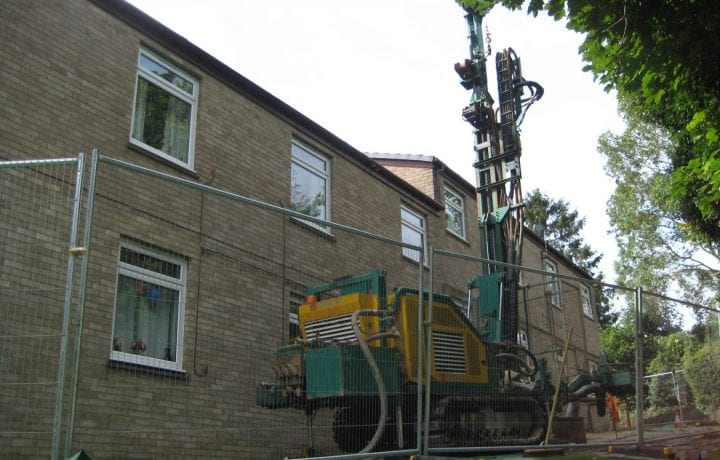
Ground Source Review: Hanover, Ashfield Court flats - Borehole Drilling
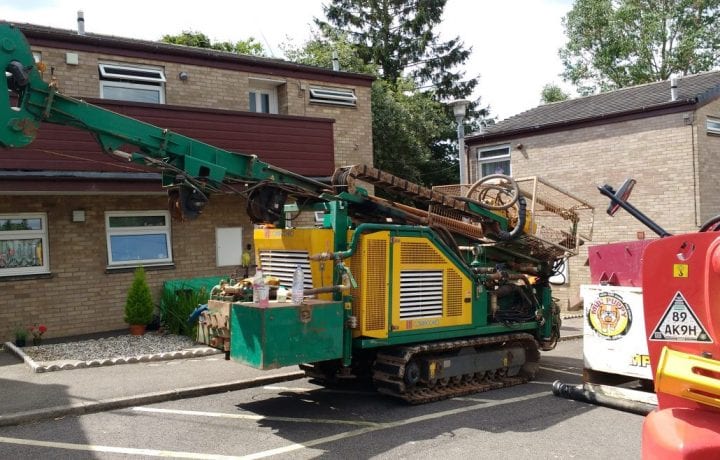
Ground Source Review: Hanover, Ashfield Court - drilling rig
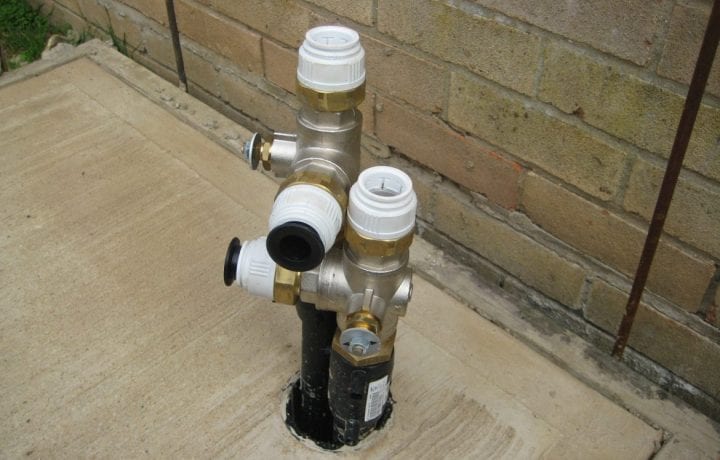
Ground Source Review: Hanover, Ashfield Court - Borehole header pipes to be connected to the heat pump
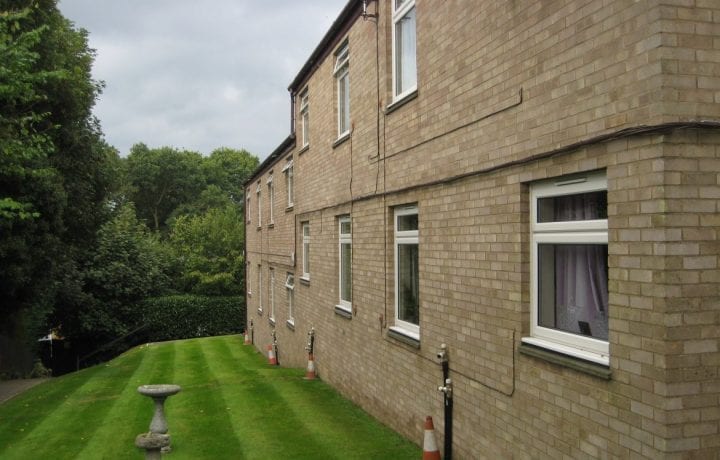
Ground Source Review: Hanover, Ashfield Court - After the boreholes were drilled